How To Choose The Right Carbide Turning Insert
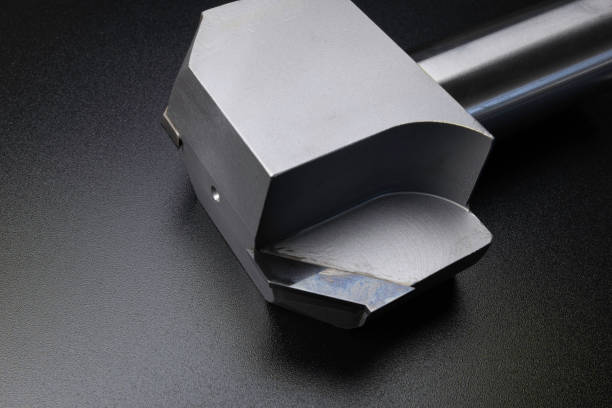
The most important factor to a successful machine machining is selecting the correct carbide turning tool insert. If you don't choose the correct insert can lead to bad results and harm to the workpiece or machine tool.
Carbide turning inserts are available in a range of shapes, sizes, and grades to suit your particular machining requirements. It can be difficult to choose the right tool for your specific task.
Grade
For accurate material machining for precise material machining, the appropriate carbide turning tool is essential. Selecting the wrong one can result in harm to the tool machine, or workpiece.
Carbide inserts are available in a range of sizes, shapes, and grades, making it easy to find the right one to meet your requirements. However, it's important to recognize that they are not all made equal.
Inserts for superalloys that are heat-resistant (HRSA) can be utilized to aid a tooling shop cut components for aerospace. Medical shops that cut biocompatible, corrosion-resistant materials like titanium or 316 stainless steel may also benefit from tools that have special coatings to decrease wear and enhance oxidation resistance.
Geometry
It is essential to ensure that the carbide turning device is designed with the proper design to function properly. This affects the chipbreaker shapes as well as the chip loads, cutting speeds as well as the surface finish, vibration, and the load on the chip.
To select the best diamond shaped carbide insert you have to be aware of how it works on your lathe, and the type of materials you are machining. You should also know what chipbreaker type is best suitable for the job you are trying to accomplish.
Many manufacturers will provide several different designs and types of inserts that can be used in a variety of applications. This could make it difficult for customers.
Nose Angle
Because it affects the machining process, the nose angle (entry/lead) of a turning inserts is essential. It may influence the surface finish chip breaking, insert strengths, as well as other variables. It can also have a significant impact on cutting forces.
High nose angles offer superior insert strength and are comparatively strong, but they require more power and may create vibrations when the machining. A nose angle that is low is, however, is less strong but creates smaller engagements with cutting edges. This leads to lower vibrations and more sensitive to heat.
The radius of the nose should be selected based on the cut's depth, feed as well as the desired surface appearance. The larger the nose radius, the more forces tangential and radial be applied to the cutting edge. This could cause uneven surface finish and chattering.
Size
Carbide inserts come in a variety of sizes. It is important to choose the correct size for your needs. They also differ in depth of cut and machine specification requirements.
Carbide inserts should be able of handling massive pieces of metal. For heavy machine work, it's suggested to select an insert that has an overall diameter of more than IC 25mm.
Carbide inserts are a common option for cutting a variety of types of materials. They also have an excellent surface finish compared to conventional cutting tools.
Coating
Carbide inserts are sometimes coated to increase hardness and lubricity, or to lower the temperature associated with cutting. These coatings are typically made using thermal CVD or, for certain applications, with mechanical PVD at lower temperatures.
For the machining of ferrous materials, such as cast iron, iron, steel and super alloys like titanium, carbide inserts coated with a coating can be utilized. The insert's durability is increased due to the heat barrier that is created by these coatings.
Common coatings for carbide inserts include TiN (titanium-nitride) as well as TiC (titanium carbide) and TiAlN (titanium aluminium nitrideTiAlN is a type of titanium aluminium nitride. The type of material processed determines the thickness of the coating. It could range from 3 to 20 microns to 0.001 to 0.0000 inches.